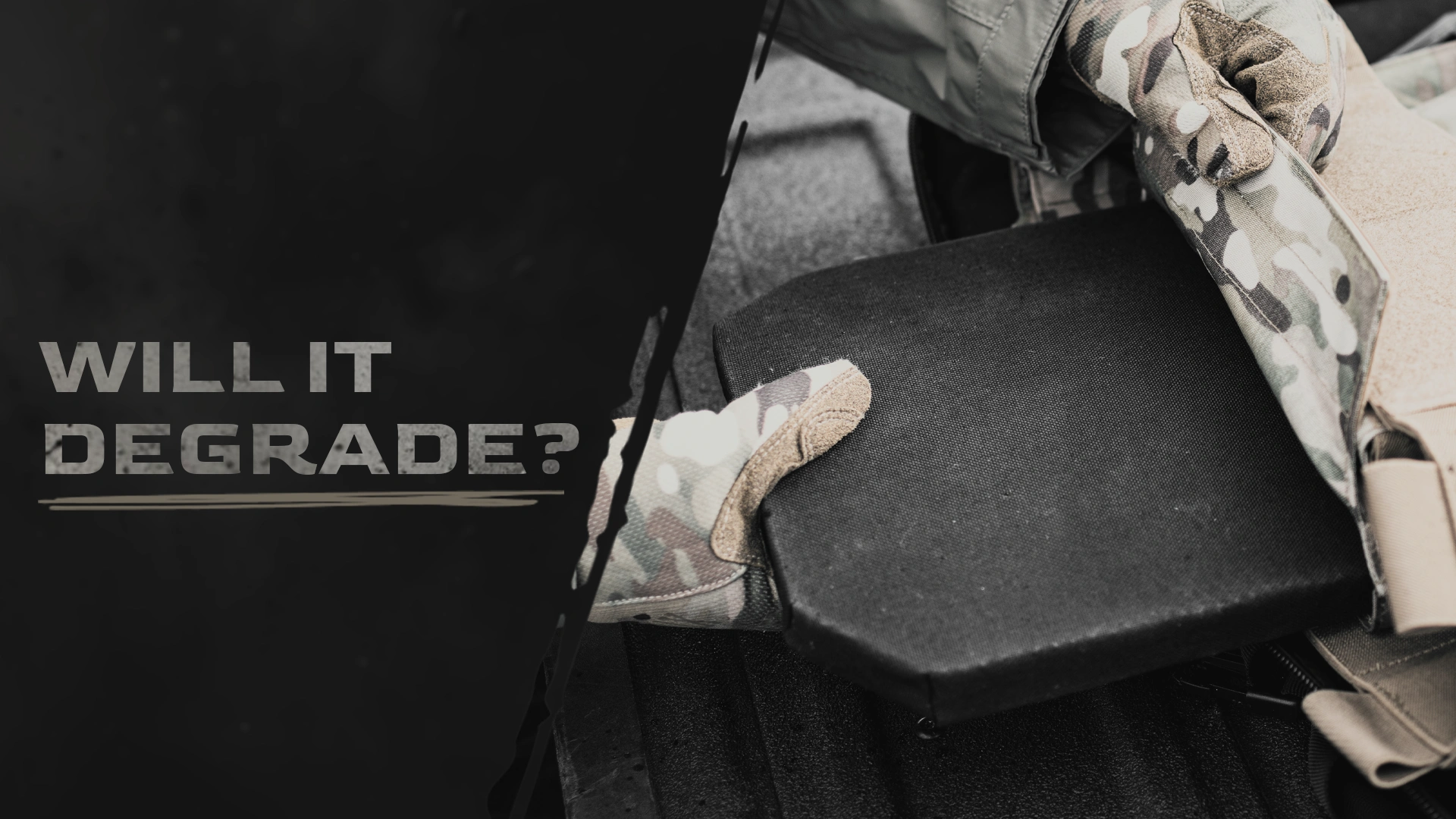
1. Introduction
Ceramic hard armor plates represent a cornerstone of modern personal protective equipment, widely adopted by military forces, law enforcement agencies, and increasingly by individuals seeking advanced ballistic protection. Valued for their relatively low weight compared to steel and their exceptional ability to defeat high-velocity rifle threats, including armor-piercing (AP) ammunition, these plates play a critical role in enhancing survivability. The development of ceramic armor dates back to early 20th-century observations, with significant operational use beginning during the Vietnam War, demonstrating substantial improvements in casualty reduction.
Despite their widespread use, a persistent question surrounds the long-term viability of ceramic armor plates during storage. Specifically, do these plates possess an inherent “shelf life” or expiration date, leading to significant degradation in protective capabilities merely through the passage of time, distinct from damage incurred through use, impact, or mishandling? This question is fueled by the common practice of manufacturers assigning warranty periods or “expiration dates,” typically ranging from five to ten years, marked on the armor itself. However, the true meaning and implications of these dates are subject to considerable debate within the industry and among end-users.
This report aims to provide a comprehensive analysis of this issue, examining the materials and construction of ceramic armor, relevant industry standards, potential degradation mechanisms, the influence of storage conditions, and available evidence regarding long-term performance. By synthesizing information from material science principles, manufacturer specifications, standards bodies like the National Institute of Justice (NIJ), technical studies, and expert analyses, this report seeks to determine whether ceramic hard armor plates inherently expire or degrade significantly due to long-term storage and to identify the key factors influencing their functional longevity.
2. Anatomy of a Ceramic Hard Armor Plate
Understanding the potential for degradation requires a foundational knowledge of how ceramic armor plates are constructed and function. These are typically composite systems designed to defeat high-velocity projectiles through a combination of material properties and structural interaction.
Function: The fundamental principle involves a hard ceramic layer, known as the “strike face,” positioned on the exterior surface. Upon impact, the extremely hard ceramic material fractures, erodes, and blunts the incoming projectile, absorbing and dissipating a significant portion of its kinetic energy. The ceramic effectively shatters the bullet. This process distributes the impact load over a larger area. Behind the ceramic strike face lies a backing layer made of a more ductile material, typically a fiber-reinforced composite or, less commonly, metal. This backer serves the critical functions of containing the fragments of both the shattered ceramic and the projectile remnant, preventing them from injuring the wearer, and absorbing the residual kinetic energy.
Common Ceramic Strike Face Materials: Several types of advanced ceramics are commonly used for strike faces, each offering a different balance of performance, weight, and cost:
- Alumina (Aluminum Oxide, Al2O3): This is the most widely used ceramic armor material, particularly in plates intended for the private and law enforcement markets. Its prevalence stems from its wide availability, relative ease of shaping into complex forms, and significantly lower cost compared to other armor ceramics; a typical 10×12 inch alumina strike face for a Level IV plate might cost the manufacturer around $20. Common grades include AD85. However, alumina has a higher density (typically around 3.4-3.9 g/cc) than other options, resulting in a lower performance-to-weight ratio. RMA Defense’s Model 1155 Level IV plate is an example using an Alumina Oxide ceramic composite.
- Silicon Carbide (SiC): Often considered to offer the most favorable balance of price and performance against a broad range of threats. It is considerably lighter than alumina (density typically around 3.1-3.2 g/cc) and demonstrates superior ballistic performance. SiC is used to protect against both smaller projectiles (like bullets) and larger ones, finding application in body armor and helicopter armor. Commercial examples include Hexoloy® and various sintered SiC formulations.
- Boron Carbide (B4C): This is generally the hardest and lightest of the common ceramic armor materials (density typically around 2.5 g/cc), offering the highest level of protection on a weight basis, particularly against smaller projectiles. However, it is also the most expensive. Reaction-bonded boron carbide (RBB4C) is a variant developed for lower-cost processing, resulting in a ceramic-metal composite containing B4C, in-situ formed SiC, and residual metallic silicon; its performance can be influenced by the weaker silicon phase. Commercial examples include CeraShield™ Boron Carbides and Schunk’s SafeGuard-B4C.
- Other Materials: Less common materials like Titanium Diboride (TiB2) and various proprietary or advanced ceramic formulations are also used.
Table 1: Comparison of Common Ceramic Armor Materials
Feature | Alumina (Al2O3) | Silicon Carbide (SiC) | Boron Carbide (B4C) |
Typical Density (g/cc) | ~3.4 – 3.9 | ~3.1 – 3.2 | ~2.5 |
Hardness (GPa) | ~14+ (Vickers) | Higher than Alumina | Highest among common types |
Compressive Strength | High | High | High |
Relative Cost | Lowest | Moderate | Highest |
Key Pros | Affordable, widely available, easy to shape | Good balance of price/performance, lighter than Alumina | Lightest weight, highest hardness |
Key Cons | Heaviest, lowest performance-to-weight ratio | More expensive than Alumina | Most expensive, potentially more brittle |
Backing Layer Materials and Function: It is crucial to reiterate that ceramics are never employed as standalone armor solutions. The backing layer is indispensable for overall performance.
- Ultra-High Molecular Weight Polyethylene (UHMWPE): Materials like Dyneema® and Spectra offer extraordinary specific strength (strength per unit weight), which translates directly to high ballistic performance in backing layers. UHMWPE enables the creation of the most lightweight armor plates at any given protection level. However, high-performance grades are expensive. UHMWPE backers are typically combined with relatively “soft” resin systems, which may lead to greater backface deformation and potential delamination compared to other backers. It is widely used in modern ceramic composite plates.
- Aramid Fibers (e.g., Kevlar®): Aramid fibers, such as Kevlar®, are another common choice for backing materials, often used in combination with ceramic strike faces. They offer good ballistic performance and deformation resistance, positioned between fiberglass and UHMWPE in terms of specific strength and cost. Concerns exist regarding potential long-term degradation, particularly through hydrolysis if exposed to moisture.
- Fiberglass (E-glass, S-glass): Composed of glass fibers (like E-glass or S-glass) embedded in resins (commonly phenolic, vinyl ester, or epoxy). Fiberglass is the most economical composite backing material, enabling the production of low-cost armor plates. However, it has significantly lower specific strength and ballistic performance compared to UHMWPE and aramid fibers, resulting in heavier plates for a given protection level.
Table 2: Comparison of Common Backing Materials
Property | E-Glass Fiber | S-Glass Fiber | Aramid (Kevlar® KM2 Plus) | UHMWPE (Dyneema® SK99) |
Density (g/cc) | 2.6 | 2.48 | 1.44 | 0.97 |
Ultimate Tensile Str. (MPa) | 3450 | 4750 | 3400 | 4100 |
Modulus of Elasticity (GPa) | 72.4 | 90 | 81 | 155 |
Elongation at Break (%) | 4.8 | 5.7 | 3.8 | 3.5 |
Normalized Specific Str. | 1 | 1.44 | 1.78 | 3.19 |
Relative Ballistic Perf. | ● | ●● | ●● | ●●●● |
Relative Cost | 1 | 2 | 4 | 8+ |
Key Pros | Lowest cost | Moderate cost | Good performance | Highest performance-to-weight |
Key Cons | Heaviest | Heavy | Higher cost than glass | Highest cost, potential deformation |
Construction Methods: The way the ceramic and backing materials are assembled also impacts performance and durability.
- Monolithic Plates: These utilize a single, large ceramic plate covering the protected area, which is then bonded to the backing material and inserted into a carrier. This approach can be advantageous for applications like aircraft armor where large, complex shapes are needed, but monolithic plates can be more susceptible to catastrophic failure from a single impact and may suffer performance degradation from fractures due to multi-hit damage or even mishandling.
- Tiled/Segmented Plates: This construction employs multiple smaller ceramic elements (tiles), which can be spheres, hexagons, squares, or other shapes, arranged side-by-side and affixed to the backing layer. Early designs used ceramic spheres embedded in matrices. Modern methods often involve cutting tiles and affixing them to the backer. Tiled designs aim to improve multi-hit capability by localizing damage; an impact shattering one tile may not compromise the integrity of adjacent tiles. Some manufacturers use tile composites even in Level IV plates to enhance multi-hit performance.
- Bonding Techniques: The method used to join the ceramic strike face to the backing layer is critical for the armor system’s performance and long-term integrity. Common methods involve using resins or specialized adhesives. High-quality manufacturing often employs processes like heat pressing or autoclaving (applying heat and pressure) to achieve a strong, uniform, and durable bond between the layers. In contrast, lower-cost plates might use simpler gluing techniques with adhesives that could be more prone to degradation over time or under environmental stress.
- Covering: Finally, the assembled ceramic-backer composite is typically encased in a protective, water-resistant fabric cover, often made of durable nylon (e.g., 600 Denier Cordura), to shield the internal components from moisture, abrasion, and UV light.
The construction details reveal that a ceramic plate’s performance and potential longevity are not solely dependent on the ceramic material itself. Instead, they are emergent properties of the entire system: the specific ceramic chosen, the type and properties of the backing material, the quality and durability of the adhesive bond connecting them, and the overall construction approach (monolithic vs. tiled). Evaluating potential expiration or degradation must therefore consider the interactions and potential failure points within this composite structure, not just the inherent stability of the ceramic.
Furthermore, the selection of materials inherently involves balancing cost, weight, and performance. Alumina strike faces paired with fiberglass backers represent the most affordable end of the spectrum, suitable for budget-conscious markets but resulting in heavier plates. Conversely, combinations like Boron Carbide with UHMWPE backing offer the highest performance-to-weight ratio, critical for demanding military or tactical applications, but come at a substantial cost premium. Silicon Carbide often occupies a middle ground, providing good performance and weight savings over alumina at a more moderate cost. This established hierarchy influences material choices and may also impact the level of quality control and bonding technology employed, particularly in lower-cost offerings, which is relevant when considering long-term durability.
3. Defining “Expiration”: Warranty vs. Service Life
The term “expiration date” as applied to body armor, particularly ceramic plates, is a significant point of confusion and contention. Understanding the distinction between manufacturer warranties, regulatory guidelines, and the actual physical service life of the armor is crucial.
Manufacturer Warranty Practices: It is standard industry practice for manufacturers of body armor, including ceramic plates, to assign a warranty period to their products. This period is typically indicated on a label affixed to the armor plate. The duration of these warranties commonly ranges from five to ten years. Specific examples found in product descriptions or care guides include 5 years, 5-7 years, 7-8 years, and 10 years. Some retailers may even offer lifetime warranties, though these often pertain to replacement after being shot, not age-related degradation. In contrast, steel armor plates are often advertised with a much longer warranty, typically 20 years.
National Institute of Justice (NIJ) Standard 0101.06 Requirements: The NIJ plays a significant role in setting performance standards and testing protocols for ballistic-resistant body armor used by U.S. law enforcement. The current standard, NIJ 0101.06, influences manufacturer practices regarding warranties:
- Minimum Warranty: The standard requires that manufacturers whose products are certified and listed on the NIJ Compliant Products List (CPL) must declare a warranty period during which the armor is guaranteed to maintain its ballistic performance against the specified threat level. This declared warranty period must be at least five years. This five-year minimum is often interpreted as being based on the expected wear and tear associated with daily duty use by law enforcement officers.
- No Age-Based Expiration Mandate: Critically, NIJ Standard-0101.06 does not mandate a specific expiration date based solely on the age of the armor. The standard’s focus is on ensuring the armor meets rigorous performance requirements (stopping specific projectiles with limited backface deformation) when new and demonstrating sufficient durability to maintain that performance throughout the manufacturer’s declared warranty period.
- Durability Testing: To assess durability, the NIJ Compliance Testing Program (CTP) subjects armor samples to environmental conditioning protocols before ballistic testing. These protocols simulate aging and wear, including exposure to heat, moisture, mechanical wear (tumbling for soft armor, less defined for hard plates), and drop tests for hard armor plates to assess their resistance to impact damage. Passing ballistic tests after these conditioning cycles provides confidence in the armor’s ability to perform reliably during its warranted service life.
The Industry Debate: Do Properly Stored Ceramic Plates Truly Expire? The existence of warranty periods and the NIJ’s 5-year minimum requirement have led to differing interpretations regarding whether ceramic plates truly “expire.”
- Argument for “No Expiration”: A significant viewpoint, often expressed by knowledgeable vendors and users, holds that high-quality ceramic plates, manufactured using appropriate materials and techniques and maintained under proper storage conditions, do not inherently expire or lose significant ballistic capability simply due to age. Proponents of this view argue that the ceramic materials themselves are chemically inert and stable over very long periods. They also contend that modern backing materials (like UHMWPE and Aramid) and, crucially, the high-quality adhesives used by reputable manufacturers are robust and degrade extremely slowly, if at all, under ideal storage. From this perspective, the date on the plate primarily represents the expiration of the manufacturer’s warranty – a period during which the company guarantees performance and accepts liability, potentially influenced by a desire for recurring revenue through “planned obsolescence”.
- Argument for “Expiration/Shelf Life”: Conversely, many manufacturers and sources state that ceramic plates do have a limited shelf life, often aligning with the typical 5-to-7-year warranty period, and recommend replacement thereafter. This viewpoint often emphasizes that even slow degradation of materials, particularly the backing layers (cited as the reason for the 5-year life in one source) and the adhesives bonding the layers, can occur over time. This perspective implicitly accounts for the increasing probability of accumulated minor damage, exposure to non-ideal environmental conditions, or material fatigue over several years, even if the plate is primarily in storage. Manufacturer recommendations and liability concerns are central to this stance. Some also suggest that higher-level plates might have shorter lifespans due to their more advanced (and potentially less proven long-term) materials.
This analysis reveals a fundamental conflict in terminology and perspective. The core of the debate stems from the conflation of the “manufacturer’s warranty period” – a defined timeframe driven by legal, commercial, and liability considerations – with the “actual serviceable lifespan” of the armor – a physical property determined by material science, manufacturing quality, and environmental history. Manufacturers understandably emphasize the warranty period to limit their long-term liability. Material science principles, however, suggest that the constituent materials of a well-made plate, particularly the ceramic itself, are inherently stable and could potentially remain effective for decades if protected from damage and adverse environments.
The common 5-year recommendation, often linked to the NIJ’s minimum warranty requirement for certified armor, appears to function primarily as a conservative risk management benchmark. It provides a practical guideline, particularly for agencies issuing armor for daily duty use, where the consequences of failure are severe, and a degree of wear and tear is assumed. This timeframe balances risk, liability, and assumed usage patterns but does not necessarily represent a scientifically determined point of guaranteed material failure for every ceramic plate, especially those stored carefully by private users.
The NIJ standard, through its requirement for a minimum 5-year warranty and its inclusion of pre-ballistic environmental conditioning tests, provides a baseline assurance of performance and durability during the warranty period. However, it does not offer a definitive judgment on the potential post-warranty lifespan of ceramic armor based purely on storage time. The standard validates within-warranty reliability under simulated stress but does not involve testing plates naturally aged for extended durations (e.g., 10, 15, or 20 years) in storage. Therefore, while NIJ compliance indicates a robust product, it doesn’t resolve the debate about long-term storage degradation beyond the warranty.
4. Potential Degradation Pathways During Storage
While high-quality ceramic armor may be inherently stable, several potential degradation pathways could affect its integrity and performance during long-term storage, particularly if manufacturing quality is suboptimal or storage conditions are not ideal. These pathways involve both physical damage and material changes.
Physical Degradation:
- Micro-cracking: A primary concern stems from the inherent brittleness of ceramic materials. Ceramic plates are susceptible to fracture if subjected to impacts, most notably if dropped onto a hard surface like concrete. Such impacts can cause cracks or microscopic fractures within the ceramic layer. These flaws may not always be visible on the exterior surface but can significantly compromise the plate’s structural integrity and its ability to effectively stop projectiles upon impact. Detection of such hidden damage might require methods like X-ray inspection. This vulnerability to handling damage represents a significant risk during the armor’s entire lifespan, including storage.
- Warping/Shape Distortion: Although less commonly cited for hard plates compared to soft armor, exposure to extreme temperature fluctuations could theoretically cause differential expansion and contraction between the ceramic and backing layers, potentially leading to warping. More practically, improper storage methods, such as folding (if possible with certain constructions), standing plates on their edge for prolonged periods, or hanging them on inadequate hangers, can induce stress and lead to shape distortion or damage to the composite structure.
Material Stability and Chemical Degradation:
- Ceramic Inertness: The core ceramic materials used in armor (Alumina, SiC, B4C) are generally recognized for their high chemical stability and inertness under typical ambient conditions. They do not undergo chemical decomposition, oxidation (rust), or biological degradation (“rot”) in the way that organic materials or some metals might. From a purely chemical standpoint, the ceramic component itself is expected to remain stable indefinitely if protected from physical damage.
- Binder/Adhesive Integrity: The adhesive layer bonding the ceramic strike face to the backing material is frequently identified as a potential point of failure over time. The long-term stability of this bond is highly dependent on several factors:
- Manufacturing Quality: This is perhaps the most critical factor. Reputable manufacturers using advanced bonding techniques (like autoclaving or heat pressing) and high-quality, purpose-designed adhesives (often epoxy-based formulations resistant to heat and moisture) produce plates where the bond is expected to be very durable. Conversely, cheaply manufactured plates might utilize lower-grade glues or inadequate bonding processes, making them susceptible to adhesive degradation and failure over time, especially when exposed to environmental stressors.
- Environmental Exposure: Even robust adhesives can be negatively affected by adverse conditions. Prolonged exposure to extreme heat can potentially soften, weaken, or chemically degrade the adhesive, compromising the bond strength. Similarly, moisture ingress, if the plate’s protective cover is damaged or sealing is poor, can attack the adhesive interface and lead to bond failure.
- Backer Material Aging: The long-term stability of the backing material itself is another consideration:
- UHMWPE: While generally very stable, some sources suggest that subtle chemical and structural changes might occur over decades, potentially leading to very slow degradation. More significantly, UHMWPE is known to be susceptible to degradation from prolonged exposure to ultraviolet (UV) radiation (from sunlight) and potentially from extreme heat, which can affect its mechanical properties. However, studies involving accelerated aging (simulating years of exposure in a shorter time) under conditions of high heat (70°C) and humidity (76% RH) have shown high stability, with less than 10% degradation in tensile strength after approximately one year of exposure.
- Aramid (Kevlar®): Aramid fibers can potentially lose some tensile strength over very long periods. Hydrolysis, a chemical reaction with water molecules, is considered a primary degradation mechanism, making aramids sensitive to prolonged exposure to high humidity. However, like UHMWPE, accelerated aging studies found para-aramid materials to be relatively resistant to degradation under most conditions, showing significant changes only at combined high temperature and high humidity (70°C and 76% RH). Older plates using aramid backers were noted to have issues with heat degradation, though this may be less common with modern materials and bonding agents.
- Fiberglass: Fiberglass composites, using established resins like epoxy, phenolic, or vinyl ester, are generally considered stable. Specific long-term degradation mechanisms unique to fiberglass backers in armor applications were less detailed in the reviewed materials compared to PE and Aramid.
Delamination: This refers to the physical separation of the backing layer from the ceramic strike face. Delamination is a critical failure mode because the synergistic action between the ceramic and the backer is essential for stopping the projectile and managing energy. If the layers separate, the plate’s ballistic performance can be severely compromised. Delamination can result from several causes during storage: poor initial manufacturing (inadequate bonding), degradation of the adhesive over time (due to age, heat, or moisture), or physical stresses induced by flexing or warping of the plate. Maintaining uniform adhesion across the interface is vital.
Considering these potential pathways, it becomes apparent that physical damage resulting from improper handling (dropping) poses a more immediate and perhaps more probable threat to the integrity of a ceramic plate during its storage life than slow, inherent material degradation. The inherent brittleness of the ceramic component makes careful handling paramount.
Furthermore, the debate surrounding long-term degradation heavily involves the quality and resilience of the adhesives and bonding processes used in manufacturing. High-quality construction significantly mitigates the risk of spontaneous adhesive failure or delamination under proper storage. Conversely, deficiencies in manufacturing introduce a significant potential failure point that can manifest over time, particularly if the plates are exposed to adverse environmental conditions like heat or moisture. This highlights manufacturing quality as a primary variable influencing actual service life.
Finally, while the backing materials themselves (UHMWPE, Aramid) can theoretically degrade, evidence suggests this is a very slow process under ideal storage conditions. Significant degradation likely requires decades of time or exposure to accelerating factors like UV light, high humidity, or extreme temperatures. Therefore, for well-manufactured plates stored correctly, backer degradation is less likely to be the limiting factor within typical expected lifespans compared to physical damage or potential adhesive issues in lower-quality products.
5. The Critical Role of Storage Conditions and Maintenance
The environment in which ceramic hard armor plates are stored and the manner in which they are handled and maintained play a crucial role in preserving their structural integrity and ballistic performance over time. Adherence to proper storage protocols directly mitigates many of the potential degradation pathways discussed previously.
Impact of Environmental Factors:
- Temperature: Exposure to extreme temperatures, both hot and cold, is detrimental and should be rigorously avoided. High heat can accelerate the degradation of adhesives used to bond the layers, potentially leading to delamination. It can also negatively affect the properties of polymer-based backing materials like UHMWPE. Rapid temperature fluctuations might induce thermal shock in the ceramic layer, potentially causing cracking. Conversely, extreme cold could potentially make materials more brittle. Storage locations prone to temperature extremes, such as vehicle trunks (especially in summer), attics, some basements, garages, or areas exposed to direct sunlight, are unsuitable. An ideal storage temperature range is often suggested to be between 50°F and 86°F (10°C to 30°C). It is worth noting that reputable manufacturers whose products undergo NIJ certification testing subject their armor to heat cycle tests to ensure performance is not unduly affected by temperature variations, suggesting well-made plates have some resilience.
- Humidity/Moisture: Moisture is a significant enemy of composite body armor. High ambient humidity (ideally kept below 50% relative humidity) or direct water exposure can compromise the armor system in several ways. Moisture can penetrate seams or damaged covers, potentially degrading the adhesive bond between the ceramic and the backer, leading to delamination. It can promote the growth of mold and mildew on the cover and potentially within the plate structure if seals are compromised. Furthermore, moisture can directly affect certain backing materials; for instance, aramid fibers are susceptible to degradation via hydrolysis. Plates should always be stored in a dry location, and if they become damp, they must be thoroughly air-dried before storage. While the outer covers are typically water-resistant , maintaining the integrity of this cover and its seals is vital. Storing plates in airtight containers that could trap moisture is generally discouraged.
- UV Light (Sunlight): Prolonged exposure to direct sunlight should be avoided. Ultraviolet radiation can degrade polymeric materials, including UHMWPE backing layers and potentially the outer fabric cover and underlying adhesives. Storage in dark locations or opaque containers is recommended.
- Chemical Exposure: Contact with chemicals such as cleaning solvents, oils, gasoline, or other potentially corrosive substances should be prevented, as these can damage the armor materials or the outer carrier. Cleaning should only be done according to manufacturer instructions, typically involving wiping with a soft cloth, perhaps slightly damp, but avoiding harsh chemicals or machine washing.
Recommended Storage Practices: Based on mitigating these environmental risks, best practices for storing ceramic armor plates include:
- Environment: Store plates in a cool, dry, dark location with stable, moderate temperatures and low humidity. Climate-controlled environments offer the best protection.
- Positioning: The preferred method is to store plates lying flat on a shelf or other flat surface, ensuring they are adequately supported to prevent bending or warping. If storing flat is impractical, hanging the plate carrier using a wide, padded, robust hanger specifically designed for body armor is the next best option. Avoid stacking heavy objects on top of stored plates. Critically, do not hang plates on thin wire or standard wooden clothes hangers, as the weight can cause damage to the carrier or potentially the plate interface. Never fold plates or store them standing on their edge, as this can create stress points and damage.
- Handling: Reinforcing the point from Section 4, ceramic plates must be handled with care at all times to prevent accidental drops or impacts against hard surfaces. Using padded surfaces when setting plates down can help minimize risk.
Inspection and Assessment: Given the potential for hidden damage and the debate surrounding expiration dates, regular and careful inspection is a critical component of responsible armor management.
- Visual Checks: Routinely examine the plate and its cover for any obvious signs of damage. This includes looking for cracks, chips, or dents in the plate surface (if visible), warping or changes in shape, frayed fabric on the cover, separation of seams or stitches, and any compromise of the cover’s sealing. However, it is important to recognize that a visually intact appearance does not guarantee internal integrity.
- Tap Test: This simple test helps assess the bond between the ceramic strike face and the backing layer. The procedure involves holding the plate with the back (wearer) side facing up and tapping firmly around the outer edges (about two inches apart) with a solid object like a screwdriver handle or pocket knife, working inwards. A clear, resonant “chime” or ringing sound generally indicates good lamination. A dull “thud” sound may suggest potential delamination or separation between the layers. Tapping the very center or directly on labels should be avoided as these areas may produce misleading sounds.
- Torque Test: This test assesses both potential cracks in the ceramic and delamination. It involves firmly grasping opposite corners of the plate (e.g., top-left and bottom-right) and attempting to gently twist or flex the plate. This is repeated with the other pair of corners. Additionally, pressing firmly around the edges while holding the plate against the body can help detect issues. Any sounds of crumbling, grinding, or rattling, or any noticeable “give” or excessive flex during the test, can indicate potential cracks or separation.
- Frequency: Inspection frequency recommendations vary. Some suggest inspecting before and after each use, and at least monthly if in storage. Others recommend annual inspections or simply periodic checks. A prudent approach involves regular visual checks combined with tap and torque tests performed periodically (e.g., annually or semi-annually) for stored plates.
The emphasis across multiple sources on specific storage protocols underscores a key point: disciplined storage and handling practices are likely more influential in determining the actual serviceable lifespan of a ceramic plate than the mere passage of calendar time. By controlling the environmental factors (temperature, humidity, UV) and preventing physical damage (drops, improper positioning), users actively mitigate the known degradation pathways. This suggests that longevity is not just an inherent property but something that is actively maintained through proper care.
Furthermore, the potential for hidden damage (micro-cracks from impacts, delamination from adhesive issues) makes routine inspection an indispensable risk management tool. Since relying solely on a warranty date is contentious, and visual inspection alone is insufficient, performing checks like the tap and torque test provides users with a practical, albeit not infallible, means to assess the continued integrity of their armor, particularly if considering use beyond the manufacturer’s warranty period.
Finally, while a single, brief exposure to adverse conditions (like leaving plates in a hot car for a short time) might not catastrophically damage a well-made plate, it is logical to assume that repeated or prolonged exposure to suboptimal conditions has a cumulative degrading effect. Heat cycles, humidity fluctuations, UV exposure, and even minor flexing or impacts during handling likely contribute incrementally to the aging of adhesives and backing materials over the long term. This reinforces the importance of consistent adherence to best practices for storage and handling throughout the armor’s life.
6. Evidence on Long-Term Performance
Evaluating the claim that properly stored ceramic armor does not expire requires examining the available empirical evidence, including standardized testing, specific studies on aged armor, and real-world observations.
NIJ Environmental Conditioning Tests: As mentioned previously, the NIJ certification process (Standard 0101.06) includes subjecting armor samples to environmental conditioning protocols designed to simulate aging and wear before they undergo ballistic testing. These tests include exposure to thermal cycles (heat and cold), humidity, mechanical wear (tumbling for soft armor), and drop tests for hard armor plates. Armor must pass the ballistic requirements after undergoing this conditioning. This provides a degree of confidence that certified armor possesses baseline durability to withstand environmental stresses expected during its warranted service life. However, these are accelerated tests simulating typically five years of use and do not directly replicate the effects of potentially decades of quiescent storage. Broader military standards like MIL-STD-810 also define rigorous environmental testing protocols used by the Department of Defense for various equipment, including potentially armor systems.
Analysis of Studies and Reports on Aged/Stored Ceramic Armor: Direct studies on the long-term storage effects on modern ceramic armor are limited, but some relevant data points exist:
- British Combat Body Armour (CBA) Study (2007): Several sources reference a study examining the performance of older British CBA plates. This research tested plates with production dates spanning 12 years, with the oldest batch manufactured in 1995 (making them 12 years old at the time of the 2007 study). Notably, the oldest batch included “damaged reject plates” with visible external damage and confirmed internal micro-fractures identified via X-ray. Despite their age and pre-existing damage, these plates reportedly still performed, on average, 12% above the required contract/design specifications. The study concluded that “No evidence was found of any construction effects, defects or deterioration due to age that resulted in a reduction in ballistic performance”. This study is frequently cited as strong evidence against inherent age-based degradation for well-constructed ceramic armor.
- Vietnam-Era Plate Tests: Anecdotal evidence, often in the form of online videos, shows functional tests being performed on ceramic armor plates dating back to the Vietnam War era (e.g., Ground Troops Variable Body Armor issued around 1969). These plates, potentially over 50 years old, have been shown to still stop period-relevant ammunition (.30 cal ball) in these informal tests. While lacking scientific rigor, these demonstrations lend support to the argument that the core materials in ceramic armor can remain stable and functional over very extended periods. One source also mentions 1967-manufactured plates being deemed ballistically viable in the early 1990s.
- Field Use Studies: Some research, like a report by the Police Executive Research Forum (PERF), has examined the performance of body armor vests used by officers in the field over time. These studies sometimes suggest a potential loss of armor performance over years of service. However, such findings inevitably conflate the effects of storage time with the impacts of daily wear and tear, exposure to varied environmental conditions (sunlight, sweat, rain), physical stresses from movement, and potentially inconsistent maintenance practices. Therefore, these studies are less directly applicable to assessing degradation solely due to quiescent storage under controlled conditions.
- British Enhanced Combat Body Armour (ECBA) Recall (2024): A recent and significant counterpoint is the urgent recall of approximately 120,000 sets of British ECBA plates. These plates, some in service since the 1980s with replacement plans repeatedly delayed, reportedly failed safety tests after scans revealed microscopic cracks in the ceramic. One in ten plates were said to have failed tests. This incident highlights that, over a very long service life (potentially involving decades of use, handling, and storage under varying conditions), physical degradation like micro-cracking can become a systemic issue in ceramic armor, compromising safety and necessitating replacement. This underscores the real-world limitations and potential failure modes of aging ceramic armor, contrasting with claims of indefinite lifespan.
- Military Inspection Policies: Some military organizations may rely on periodic inspections and condition assessments rather than strictly adhering to fixed replacement schedules based on age or warranty expiration. The US Army, for example, has policies for inspecting hard armor inserts to identify potential failures. This practice suggests an acknowledgment that actual condition, rather than just age, is a critical determinant of serviceability.
Expert Perspectives and Field Observations: Opinions from industry experts and vendors often reflect the dichotomy discussed earlier. Many emphasize the distinction between warranty expiration and actual service life, arguing that quality plates last well beyond their warranty if cared for. Personal accounts exist of disassembling 10+ year old used ceramic plates (from reputable US manufacturers) and finding no signs of degradation – strike face intact, no delamination, strong adhesives. However, these are contrasted with examples of older, poorly constructed plates (like the TAP Gamma plates mentioned in one source) that suffered from delamination and adhesive failure over time, potentially leading to ballistic failure.
Evaluating the available evidence leads to several observations. Firstly, there is a scarcity of large-scale, scientifically rigorous, long-term studies that specifically isolate the effect of storage time alone on the ballistic performance of a wide range of modern ceramic armor plates (various materials, manufacturers, bonding techniques) under controlled conditions. Much of the argument for longevity relies on extrapolating from the known stability of ceramic materials, accelerated aging tests, a few specific studies on older armor types (like the British CBA study), and anecdotal evidence. This lack of comprehensive, directly applicable data contributes significantly to the ongoing debate and uncertainty.
Secondly, manufacturing quality emerges as a critical, potentially confounding variable. The positive results observed in aged plates (e.g., the CBA study, Vietnam-era tests) might reflect the high quality standards of those specific military procurements or manufacturers. Conversely, failures or degradation observed in other cases (e.g., the ECBA recall, issues with poorly made plates) highlight that manufacturing defects, lower quality materials, or less robust bonding techniques can indeed lead to degradation or failure over time. This makes it difficult to generalize about the longevity of all ceramic plates based solely on age, as initial quality appears to be a major determinant of long-term stability.
Thirdly, the recent British ECBA recall serves as a stark, real-world reminder that physical degradation, specifically micro-cracking, remains a tangible concern for ceramic armor over extended service life. While the exact contribution of storage versus use and handling in that specific case is unclear, it demonstrates that ceramic plates are not immune to developing integrity issues over time. This reinforces the necessity of thorough physical inspections (Section 5), as subtle damage compromising performance might develop even if the base materials have not chemically decomposed.
7. Comparative Lifespan Analysis: Ceramic, Steel, and Polyethylene
To provide further context, it is useful to compare the aging characteristics and potential longevity issues of ceramic composite armor with the other primary types of hard armor materials: steel and standalone polyethylene (PE / UHMWPE).
Ceramic Plates (Composite):
- Lifespan/Warranty: Typically 5-10 years warranty period cited. Potential for much longer actual service life if high quality, properly stored, and undamaged.
- Primary Longevity Concerns (Storage): Susceptibility to cracking from physical impact/drops due to brittleness. Potential degradation of adhesives and/or delamination, particularly in lower-quality plates or under adverse environmental conditions (heat, moisture). Slow degradation of backing materials (PE/Aramid) possible over very long term or with UV/moisture exposure.
Steel Plates:
- Lifespan/Warranty: Generally considered the longest-lasting option, often cited with a 20-year warranty. The base material (steel) is highly stable.
- Primary Longevity Concerns (Storage): Primary concern is corrosion (rust) if the protective outer coating (e.g., anti-spall coating) is damaged, exposing the steel to moisture. Less sensitive to temperature fluctuations or UV compared to composites.
- Durability & Other Factors: Highly durable against physical impacts (not brittle like ceramic) and inherently multi-hit capable. Main drawbacks are significant weight and the risk of spalling (bullet fragmentation projecting outwards), although this is often mitigated by specialized coatings.
Polyethylene (PE / UHMWPE) Plates (Standalone): (Note: These are typically rated up to NIJ Level III or special threats, not usually Level IV standalone)
- Lifespan/Warranty: Often carry similar 5-year warranty periods as ceramic composites. The material itself may potentially last longer if well-protected.
- Primary Longevity Concerns (Storage): Known susceptibility to degradation from prolonged UV exposure (sunlight) and potentially extreme heat, which can affect the polymer structure. Potential for very slow chemical degradation over decades. Less susceptible to cracking from drops compared to ceramic, but can potentially deform.
- Durability & Other Factors: Offer the lightest weight for a given protection level (up to Level III). Inherently multi-hit capable and often positively buoyant. Can exhibit greater backface deformation than ceramic or steel.
Table 3: Comparative Longevity Factors of Hard Armor Types
Feature | Ceramic Composite | Steel | Standalone PE/UHMWPE |
Typical Warranty | 5-10 years | 20 years | 5 years (similar to ceramic) |
Primary Degradation Concerns (Storage) | Cracking from impact (brittle), Adhesive/bond failure, Delamination | Corrosion/Rust (if coating damaged) | UV degradation, Heat sensitivity, Slow chemical aging |
Key Environmental Sensitivities | Extreme Temps, Moisture, Impact | Moisture (if coating breached) | UV Light, Extreme Heat |
Relative Durability (Handling) | Fragile (can crack if dropped) | Very Durable | Less fragile than ceramic, can deform |
Relative Weight | Lighter than steel, heavier than PE | Heaviest | Lightest |
Key Advantages (Longevity) | Inert ceramic material, robust if well-made & handled carefully | Very long shelf life, robust against handling damage | Lightweight (less stress on user/storage) |
Key Disadvantages (Longevity) | Brittleness requires careful handling, Lifespan depends heavily on quality & storage | Potential for corrosion if damaged, extreme weight | Environmental sensitivities (UV, heat) require careful storage |
This comparison highlights that no single hard armor material offers a perfect solution regarding long-term storage and durability; each presents a unique profile of risks and benefits. Ceramic composites offer excellent protection-to-weight ratios against high-level threats but demand careful handling due to their brittleness and rely heavily on the quality of their construction (particularly the adhesive bond) for long-term integrity. Steel provides exceptional durability against handling damage and a very long potential lifespan but suffers from extreme weight and the risk of corrosion if its protective coating is compromised. Standalone polyethylene offers the ultimate in lightweight protection (up to its threat level rating) but requires diligent protection from environmental factors like UV light and extreme heat.
Therefore, the commonly cited shelf life figures (5-10 years for ceramic/PE, 20 years for steel) should be interpreted as general guidelines reflecting typical warranty practices and the relative inherent stability and vulnerabilities of the materials, rather than as absolute expiration dates dictating guaranteed failure. For all types of armor, the actual functional lifespan achieved in practice is highly contingent upon the initial manufacturing quality, the history of handling and potential impacts, and the consistency of adherence to proper storage conditions.
8. Conclusion and Recommendations
Synthesis: Do Ceramic Plates Degrade Significantly Solely Due to Long-Term Storage?
Based on the analysis of material properties, manufacturing processes, industry standards, available empirical evidence, and expert perspectives, the central question can be addressed with nuance. High-quality ceramic hard armor plates, manufactured by reputable companies using stable materials (inert ceramics, durable backing materials like UHMWPE or Aramid, and robust, modern adhesives) and appropriate bonding techniques (e.g., autoclaving), do not appear to experience significant degradation in their intrinsic ballistic performance solely due to the passage of time when maintained under ideal storage conditions. Ideal conditions entail a cool, dry, dark environment, free from physical stress or impact. The core ceramic materials are chemically stable, and degradation of quality adhesives and backing materials under these conditions is likely extremely slow.
However, this conclusion comes with critical caveats. It applies primarily to high-quality plates stored ideally. The practical reality is influenced by several factors:
- Manufacturing Variability: Lower-quality plates may utilize inferior adhesives or bonding processes, making them susceptible to degradation (e.g., delamination) over time, even in storage.
- Storage Imperfections: Real-world storage may deviate from the ideal, potentially exposing plates to temperature fluctuations, humidity, UV light, or minor physical stresses that can accumulate damage over years.
- Handling Damage: The inherent brittleness of ceramics means that accidental drops or impacts at any point during the plate’s life, including during storage or handling, can cause potentially undetectable micro-cracks that compromise performance.
- Warranty and Liability: The commonly cited 5-to-10-year “expiration date” or warranty period serves as a practical timeframe established by manufacturers to limit liability and align with NIJ’s minimum requirements for duty gear. It represents a period of guaranteed performance under expected (often daily duty) use conditions, rather than a definitive point of material failure for all plates under all circumstances.
Therefore, while inherent chemical decomposition due to age alone seems unlikely for well-made, well-stored plates, the probability of encountering performance-degrading factors (accumulated environmental exposure, potential adhesive aging in some products, undetected physical damage) increases over time.
Key Factors Determining Ceramic Armor Longevity:
The actual functional lifespan of a ceramic armor plate is determined by a combination of factors, with the following being most critical:
- Manufacturing Quality: This is arguably the most important factor. The choice of materials, the type and application of adhesives, the bonding process (heat pressing, autoclaving), and overall quality control significantly influence the plate’s initial integrity and its resistance to degradation mechanisms like delamination.
- Storage Conditions: Consistent adherence to proper storage protocols – maintaining a stable, cool, dry, dark environment – is essential to minimize environmental degradation of adhesives and backing materials.
- Handling Practices: Due to ceramic brittleness, careful handling to avoid drops, impacts, or improper flexing is crucial throughout the plate’s life to prevent physical damage.
- Material Selection: While standard armor ceramics are stable, the specific combination of ceramic, backer, and adhesive system influences the plate’s overall robustness and potential vulnerabilities (e.g., UHMWPE’s sensitivity to UV/heat vs. Aramid’s sensitivity to hydrolysis).
Recommendations:
Based on this analysis, the following recommendations are provided for managing ceramic hard armor plates:
- Procurement:
- Prioritize purchasing plates from reputable manufacturers with established track records, transparent material specifications, robust quality control processes, and potentially longer warranty periods.
- Consider NIJ 0101.06 certified products as they provide assurance of meeting baseline performance and durability standards, including environmental conditioning tests.
- Understand the trade-offs associated with different material combinations (Alumina vs. SiC vs. B4C; Fiberglass vs. Aramid vs. UHMWPE) in terms of cost, weight, performance, and potential vulnerabilities.
- Storage:
- Implement and enforce strict storage protocols based on manufacturer guidelines and established best practices: store flat or on appropriate hangers in a cool, dry, dark, climate-controlled environment whenever possible.
- Protect plates from physical impacts, excessive weight/pressure, and environmental extremes during storage and transport.
- Inspection:
- Institute a program of regular, documented inspections for all ceramic armor plates, irrespective of age or warranty status.
- Inspections should include thorough visual checks for external damage, plus tactile assessments like the tap test and torque test to detect potential delamination or internal cracks.
- Any plate that fails inspection (shows cracks, chips, warping, delamination via tap/torque test) or has sustained a significant impact (e.g., dropped on a hard surface) should be immediately removed from service and replaced.
- Replacement Policy:
- High-Risk / Duty Use (Military, Law Enforcement): It is strongly recommended to adhere to the manufacturer’s stated warranty period for replacement. This conservative approach aligns with NIJ guidelines, manages liability, and prioritizes maximum safety assurance for personnel facing regular occupational hazards. Immediate replacement upon damage or failed inspection is mandatory.
- Low-Risk / Personal Use (Private Sector): Using plates beyond the manufacturer’s warranty period may be considered, but only if the following conditions are met: the plates are from a known high-quality manufacturer, they have a documented history of meticulous storage under ideal conditions, they have never been dropped or subjected to significant impact, and they consistently pass regular, thorough inspections (visual, tap, torque). The user must understand and accept the potential risks associated with using equipment beyond its guaranteed performance period. If any doubt exists about the plate’s condition, replacement is the prudent course of action.
- Future Research: There is a clear need for more independent, large-scale, long-term scientific studies specifically designed to evaluate the effects of extended storage (e.g., 10, 15, 20+ years) under controlled environmental conditions on the ballistic performance of modern ceramic armor plates from various manufacturers and material compositions. Such research would provide more definitive data to inform replacement policies.
Ultimately, the decision of when to replace stored ceramic armor involves balancing the scientific understanding of material stability against practical considerations of risk management, liability, and the potentially severe consequences of armor failure. While evidence suggests that well-made, well-cared-for plates can likely function beyond typical warranty periods, the user’s or agency’s tolerance for risk often dictates adherence to more conservative replacement schedules, particularly in professional contexts. Regardless of the stance on “expiration,” effective armor lifecycle management necessitates a proactive approach combining careful selection, controlled storage, rigorous inspection, and informed replacement decisions, rather than simply relying on a date printed on a label.